(PDF) Analysis of material flow and consumption in cement ...
The results show that approximately 2.48t, 4.69t, and 3.41t of materials are required to produce a ton of the product in raw material preparation, clinker production, and cement grinding stages ...
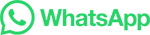