Material Model Case Study | Mining Industry Process ...
Specifically, the solid feed rate to two ball mills could not be measured directly as the slurry is fed from a distribution box in a trough. Reconciling upstream and downstream flows allow for estimation of the total solids fed as well as the recycle ratio around the ball mills. ... ← Pipeline Pumping Case Study Thickener Case Study ...
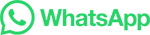