Ball Mills - an overview | ScienceDirect Topics
Recirculation factor, that is, the ratio of mill throughput to fresh feed is up to three. Beyond this, efficiency gains are minimal. 2.10.2 Vertical Mills. For more than 50 years vertical mills have been the mill of choice for grinding raw materials into raw meal. More recently they have become widely used for cement production.
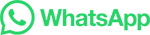