Effect of grinding depths on SiC nanogrinding behavior ...
In this paper, the nanogrinding process of single-crystal silicon carbide is studied with molecular dynamics. By changing the grinding depth, we analyze the atomic Y direction displacement, crystal defect, force, von Mises stress and the wear of abrasive. We found that with the increase in grinding depth, the atomic Y direction displacement, crystal defect, force and …
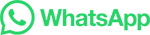