Hammermills - Sudenga Industries Inc.
Long-term maintenance costs are considerably less expensive than similar capacity roller mills. Sudenga's hammermills are available with various feed and discharge formats to fit most applications. Standard Features. 6″ x 18″ (15.2 x 45.7 cm) diameter full circle grinding chamber. Direct drive hub assembly with 15 hammers.
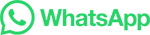