REPAIR AND MAINTENANCE SOLUTIONS - ESAB
RAW MILL SECTION 5 Vertical Roller Mill Roller/Table 6 Sinter Cast Roller 7 VRM Body Liners 8 VRM Feed Chutes KILN SECTION 9 Clinker Crusher Rolls/Hammers 1J* Kiln Tire 2J* Support Rollers CEMENT MILL SECTION 10 I.D / F.D Fan 11 Roller Press Roll 3J* Girth Gear 4J* Ball Mill Shell *Joining applications TYPICAL APPLICATIONS FOR THE CEMENT INDUSTRY.
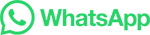