Modelling Power Consumption in Ball-End Milling Operations ...
Power consumption is a factor of increasing interest in manufacturing due to its obvious impact on production costs and the environment. The aim of this work is to analyze the influence of process parameters on power consumption in high-speed ball-end milling operations carried out on AISI H13 steel.
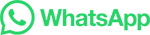