Raw Mix Preparation - ABB
lity deviations in the mill or silos, or for instance find remedy to feeders malfunctions. This permits implementation of predictive actions rather than reactive ones. Raw Mill Optimization The Raw Mill Optimization Module achieves stable mill operation at the maximum economic produc-tion rate for the fineness, moisture, and chemical
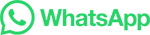