Ball Mill EDM | Mill (Grinding) | Gear
Suitable for big and small mills (Notch impact strength 4 10 J/cm2) 29 HGRS Tikaria_Mill Workshop SEPT-07 Life Time of Shell Liners 30 HGRS Tikaria_Mill Workshop SEPT-07 Grinding Media Coarse grinding 90 50 [mm] Fine grinding 50 12 [mm] 31 HGRS Tikaria_Mill Workshop SEPT-07 Grinding in Ball Mill Coarse grinding (1 st chamber) Cataracting of ...
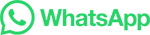