Technologies and Best Practices in Steel Rolling ...
This project on 'Energy Efficient Technologies & Best Practices in Steel Rolling Industries in Indonesia' primarily focuses on activity "3" i.e. country …
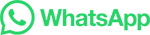
This project on 'Energy Efficient Technologies & Best Practices in Steel Rolling Industries in Indonesia' primarily focuses on activity "3" i.e. country …
practices and the maintenance of asset condition all contribute to the ability to meet these performance requirements. Some typical key performance indicators for manufacturing include operating cost; asset availability, lost time injuries, number of environmental incidents, OEE and asset utilization. Consider asset utilization, as depicted in
Coal mill pulverizer in thermal power plants. 2.Coal pulverizer/mill system One of the critical power plant components that is relied upon to convert the energy stored in coal into electricity is the coal pulverizer or mill. The coal flow is controlled by the feeder, allowing coal to flow into the pulverizer mill. The pulverized coal
Whether it's the use of a low-pressure blower instead of a high-pressure compressed air system to save energy, or a $75 million natural gas-fired Combined Heat and Power (CHP) system to replace coal as a power source at its corn wet mill in Lafayette, Indiana, Tate & Lyle is on a mission to protect the planet.
Following measures are, in general in practice for prevention and control of air pollution in mining industry: (i) Dust suppression through heavy duty sprinklers/road watering tracks is being done at various sensitive points such as haul roads, coal/ore handling points, crushing and screening plants etc.; (ii) Dust extraction facilities are ...
best practices in drill and blast 29 APRIL - 01 MAY 2014 | ROYAL ON THE PARK, BRISBANE, QLD, AUSTRALIA W: • T: +61 (2) 9229 1000 • E: [email protected] 2
Here's to you…and your future. Being a CooperVision Best Practices honoree means more than just taking home a plaque. You become part of a family that has your back — a network of practitioners who share insights into their brilliance, a new avenue to build your practice via digital and public relations support, and a community of like-minded professionals eager to see you …
Gearless mill drive (GMD) and digital services help increase production by 50% at Kinross Tasiast mine in Africa. Driving Boliden's electric transformation, saving 830 m3 of diesel annually and reducing emissions by 80 %. Sustainable deep underground mining: LKAB, ABB, Epiroc, Combitech and AB collaboration.
Best Practices Manual for Indian Supercritical Plants Partnership to Advance Clean Energy – Deployment (PACE-D) PACE-D Technical Assistance Program February 2014 This report is made possible by the support of the American People through the United States Agency for International Development (USAID).
Best Practices for the Design and Operation of Coal Mill Dust Collectors Monday, October 7, 2019 by Filtration Team Today, cement manufacturing plants have to contend with a double-edged sword: How do they …
Standard practices suggest a minimum airstream velocity within any duct of 3500 feet per minute (fpm), and between 4000 and 4500 fpm for heavier dusts, such as sand. Should the dust travel at lower than adequate velocities, it will tend to settle and accumulate in the ducts choking the system. This restriction of
Tips & Best Practices Stock Item Book Sales and Purchase Policies ... Our conversion of aging coal systems to cleaner-burning natural gas has resulted in a variety of measurable clean air benefits, including helping us reduce greenhouse gas emissions from our pulp and paper mills by 27 percent since 2013.
Spring 2019 Fossil Best Practices Awards. The Fossil Best Practices Awards were established by the EUCG Fossil Generation Committee as part of its mission to share best demonstrated practices that continuously improve safety, environmental responsibility, reliability, and economics in coal, oil, and gas fleet generation.
coal like coalification degree, petrographic composition, moisture content, mineral content, particle size, pyrite content are discussed independently. 1. Introduction Like gas and liquid fuel, coal is a material which can be stored in large quantities because of some necessities. Although stacking is generally done in open areas, there
To achieve good combustion and satisfactory flame formation, coal needs to be dried and ground to a proper degree of dryness and fineness. Drying of moisture in coal is achieved normally by ducting part of the kiln exhaust gas through the mill with inlet temperatures of …
These best practices are enforced to minimize plug exposure time, which in turn maximizes the probability of plug utilization success. ... Fully mechanized top …
Standard to adopt as a relevant Standard, or best practice to increase the efficiency, reliability, and safety of the process. ... bunker the coal flows through coal mills to boiler furnace. The main aim of CHP to maintain level of coal in bunkers for smooth coal supply to …
Best Practices User Guide. iii Reference Manual 00809-0700-4530, Rev AA September 2013 Rosemount Process Radar in Power Applications Best Practices User Guide ... Coal mill supply silo (bunker) Coal stack pile and other fuel sources (bark, garbage) 1.7 Fuel combustion / …
NCL is committed to provide energy security to the country by attaining environmentally & socially sustainable growth through best practices from mine to market. Systematic coal mining in Singrauli Coalfield started in 1964 by erstwhile NCDC. Jhingurdah OCP was the first mine which started producing coal from 1966-67.
The Crédit Agricole group is comprised of a banking arm, an insurance division, and asset management giant Amundi. The group excludes all companies developing new coal assets and is one of the few financial institutions to also exclude companies purchasing existing coal assets without pledging to shut them down by their planned end of life by 2030 in EU/OECD countries …
Past practice for coal washing-plant slurries generated at some strip-mining operations in the Midwest was disposal in successive rows of old spoil banks or, more commonly, in the last furrow of such mines. ... Mill Tailings. Ore or mineral milling or concentration can be performed by a number of methods, such as gravity concentration, magnetic ...
Safe coal handling practices are designed to ensure that the fuel remains intact throughout its journey from the mine until the point at which it is ignited in the boiler. It takes as little as 1.4 kg (3 lbs) of pulverised coal in 28 m3(1,000 ft3) of air to form an explosive mixture.
Insuring Best Practices. By. -. 6.1.2005. Insurance companies expect power plant owners to follow preventive maintenance best practices to …
in the mining or coal processing operations. Fig.3 Mill fuel piping connections to furnace. II. COAL MILL SPECIFICATIONS & PERFORMANCE ANALYSIS Typical Coal Pulveriser Mill Details in 660 MW Super-Critical [3] Unit is as given in table Table No. 1. Table.1 Coal mill Type Bowl Type Medium-speed Coal mill Number of Mills 6set/ boiler
Unit's Best Practices Replication of Kaizens –Major Process Fan Inlet Box Modification Preheater, Raw Mills, Coal Mill, etc. Conversion of Coal Mill & Cement Mill ESP to Bag house to reduce emissions to < 20 Mg/Nm3 Ever highest kiln refractory life achieved in Line-2 : 11.3 Months Ever highest Burner refractory life achieved in Line-2: 13.4 ...
desired or optimum result." To a certain extent, the concept of "best practice" can be understood as "best policy measures" or (in a broader context) "best policy and measures" to secure the recovery and use of coal associated gases, primarily coal mine methane (CMM) and coalbed methane (CBM), which are obtained through pre-mine ...
Best ppt on Presentation on Coal handling plant 1. 30 June 2013 1 Prsentation On Coal Handling Plant (CHP) ... size become 80mm. This coal is again fed to the crusher and the size become less than 20 mm or 20mm. Then this coal is fed to the coal mill for pulverization. Even when the bunker is full this coal is used for stacking or storage of ...
Best Practices in 3 Axis Machining. 3 Axis machining is THE MOST common application for all of MecSoft's CAM milling plugins. The reason is quite simple. This suite of toolpath strategies can quickly and accurately machine a vast majority of components and tooling required by …
and provide a framework to facilitate consistent categorization of coal quantities found within various depositional and tectonic regimes. With respect to coal MRMR estimation and reporting, the standards in GSC Paper 88-21 supersede the preceding Best Practice Guidelines. GSC Paper 88-21, includes some
The Ball Mills are on a schedule of 4-monthly overhaul. The main job is the repair or replacement of the lifters and liners, but other work is carried out on the mill to ensure its reliable operation over the following 4 months. In addition, preventive maintenance is carried out on other units in the stream (e.g. the conveyors).
حقوق النشر © 2024.Artom كل الحقوق محفوظة.خريطة الموقع