Pulverized Coal Pipe Testing and Balancing
Collecting coal samples using an isokinetic probe provides the best data describing actual operating conditions inside the coal pipe. Source: Storm Technologies Inc. The isokinetic coal sampling method, although more difficult, is the best option for determining the true mill coal fineness produced and to calculate pulverizer performance.
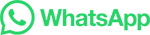