Corn wet milling process flow diagram. | Download ...
Download scientific diagram | Corn wet milling process flow diagram. from publication: Bioethanol production: Feedstock and current technologies | Fossil fuels such as oil, coal and natural gases ...
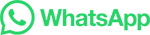