Ore Crushing and Grinding-Ore Beneficiation-
Ore Crushing and Grinding. Ore crushing and screening, grinding and classification are essential preparatory work before separation to get proper ore size. There is a balance to keep proper ore size neither too rough (insufficient liberalization) and too fine (over-crushed) in order to achieve high recovery rate and high efficiency.
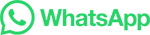