PRODUCTS - Shanghai Bogvik Wear Material Co., Ltd.
Ball Mill & Sag Mill Parts Mill Liner. Roller Tire Raymond. Roller Tire Willams. Steel Ball. Heavy Machinery Parts Bucket Tooth. Sprocket. Chocolate Bar. Track Shoes. Wear Plate. Metal Shredder Parts Hammers. Grates. Breakers and Cutter Bars. Anvils Side Liners. Caps and Hammer Pins. Pin Protectors. Feeder Wear Parts Apron Feeder Pans ...
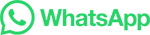