Fundamentals of Cutting
factors influencing cutting process. types of chips chip breakers cutting tool types of cutting temperature distribution tool wear mechanics of chip formation. inefficient but most important manufacturing process. machiing conditions m/c tool. ... grinding • single vs multi point ...
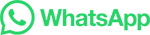