Revolution of Grinding Mill (Roller Body), Design ...
Follow. Revolution of Grinding Mill (Roller Body), Design, Operation, Maintenance and Advancements The milling of wheat into flour has been a key technology underpinning and influencing Western ...
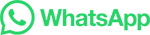