Top 10 "tips" for improving grinding efficiency of ball ...
Ball mill grinding efficiency is low, low processing capacity, high production energy consumption, product fineness is not stable and so on is most of the peers will encounter the problem.How to effectively improve the grinding efficiency of ball mill is an important problem.Below, we share 10 ways to improve the grinding efficiency of the ball mill!
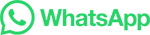