Method of Steel Grinding Ball Proportioning and Example ...
In this formula, G means the total mass of the ball(t). D is the inner diameter of ball mill cylinder(m). L is the effective length of the cylinder of the ball mill(m). ϕ is the medium filling rate(%). And δ is the bulk density of the ball(t /m …
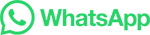