Chapter 18. Feed Milling Processes - Food and Agriculture ...
Within 20 seconds of entering the pellet mill, feed goes from an air-dry (about 10-12 percent moisture) condition at ambient temperature, to 15-16 percent moisture at 80-90°C. During subsequent compression and extrusion through holes in a ring' die, friction further increases feed temperature to nearly 92°C.
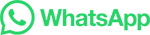