US5203122A - Method of grinding titanium - Google Patents
This invention relates to the grinding of titanium alloys and particularly to the grinding of titanium alloys using electroplated synthetic diamond wheels with surface speeds in excess of 2290 surface meters per minute. Other operating parameters are defined which permit the effective grinding of titanium at high rates and which produce desirable residual surface compressive …
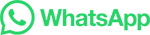