Troubleshooting roll defects - causes and corrective actions
Web wrinkling during start of the roll: Reset sheet spreading equipment. Web slack during start of the roll: Fasten web to core securely prior to winder startup. Web weaving during start of the roll: Reduce web cross-deckle caliper variation. Winding …
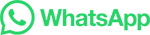