Fabrication of Transparent Y2Zr2O7 Ceramics from ...
After high-energy ball milling, the porous structure of the powder was destroyed. The Y 2 Zr 2 O 7 transparent ceramics were obtained by sintering the ball-milled powders at 1850°C for 6 h in vacuum. Ball milling of the as-burnt powders was found to play a key role on the in-line transmittance of the resultant ceramic.
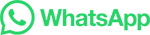