(PDF) SIZE REDUCTION BY CRUSHING METHODS
crushers and cone crushers whereas rod m ills and ball mills, closed circuited with a classifier unit, are generally employed for grinding purposes in …
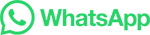
crushers and cone crushers whereas rod m ills and ball mills, closed circuited with a classifier unit, are generally employed for grinding purposes in …
Practical 1: Title: Ball Milling Objective: To grind the coarse salt to a smaller size by using a ball mill and to obtain the particle size distribution of the initial and the sieved final mixture. Introduction: 'Ball milling is a method used to break down the solids to smaller sizes or into a powder. A…
Cryo-milling was performed in an oscillatory ball mill (Mixer Mill MM400, Retsch & Co., Germany). A fresh 1 g batch of powder was used for each milling. The powder samples were placed in a 25-mL volume stainless steel milling jar containing one stainless steel ball (Ø = 15 mm). The ball/sample weight ratio was 14:1.
Bunge F., Pietzsch M., Müller R., Syldatk C. Mechanical disruption of Arthrobacter sp. DSM 3747 in stirred ball mills for the release of hydantoin-cleaving enzymes. Chemical Engineering Science. 1992; 47 (1):225–232. doi: 10.1016/0009-2509(92)80216-Y. [Google Scholar]
When using a ball nose end mill, the most critical area of the cutting edge is the tool center, where the cutting speed is close to zero, which is unfavorable for the cutting process. Chip evacuation at the tool center is critical, due to the narrow space at the chisel edge.
Milling machine is another most important machine tool after the Lathe machine tool and drilling machine.. In this machine, a multipoint cutter is rotating against the workpiece and material removed from the workpiece accordingly.. In today's article, you will learn about the definition, parts, types, and operation of a milling machine, also at the end of the article, I will add the ...
The ball mill consists of a metal cylinder and a ball. The working principle is that when the cylinder is rotated, the grinding body (ball) and the object to be polished (material) installed in the cylinder are rotated by the cylinder under the action of friction and centrifugal force.
grinding theory of ball mill [1-3] is to study the motion pattern of grinding medium and pattern of motion. The movement of the medium in the rotation body of the ball mill is a complicated process. Its movement depends on the speed of the mill …
A milligram or less of the fine-ground sample is mixed with about 100 mg of dry KBr powder in a mortar or ball mill. . The mixture is compressed in a die to form a transparent disk. 4.3.6. Mulls. . A few milligrams of the powdered sample are ground with a mortar or with pulverizing equipment.
The Mixer Mill MM 500 is also stated to be a real alternative to classic planetary ball mills, why is this the case? What's unique about the MM 500 is that performance, handling, application fields and design make it a combination between a classic mixer mill and a planetary ball mill.. When it comes to long-term grindings of several hours with high energy input to obtain particle sizes <1 ...
In this paper, the milling parameters of high energy ball mill (Fritsch Pulverisette 7) like vial geometry, number and size of balls and speed of the mill were modelled and discussed. Simulations through discrete element method (DEM) provide correlation between the milling parameters. A mathematical model is used to improve and develop this process.
A ball mill, a type of grinder, is a cylindrical device used in grinding (or mixing) materials like ores, chemicals, ceramic raw materials and paints. Ball mills rotate around a horizontal axis, partially filled with the material to be ground plus the grinding medium. Different materials are used as media, including ceramic balls,flint pebbles ...
A ball mill. Inside a ball mill, the balls move round in a circle as the mill turns, crushing the ore into a powder. This process of reducing the size of the rocks requires a lot of energy. Just image how hard it is to break a rock. How much more energy do you think is …
The SKF manual lubrication tools are specifically designed and selected to support lubricant storage, handling, dosing, labeling, analyzing and applying lubricants. Together, SKF and Lincoln combine more than 300 years of experience in managing lubrication and reducing friction.
Gearless mill drive (GMD) and digital services help increase production by 50% at Kinross Tasiast mine in Africa. Driving Boliden's electric transformation, saving 830 m3 of diesel annually and reducing emissions by 80 %. Sustainable deep underground mining: LKAB, ABB, Epiroc, Combitech and AB collaboration.
Ball mill is a high-energy mill process especially used for an energy-intensive process like mechanical alloying, mechanochemistry, or mechanical activation. Planetary ball mill is used to determine the dependence of process efficiency using milling parameters such as ball size and number, mill geometry, and velocity of the rotating parts.
The ball to charge ratio may be 5:1, 10:1, 15:1. This method is more efficient in achieving fine particle size. Rod mills: Horizontal rods are used instead of balls to grind. Granularity of the discharge material is 40-10 mm. The mill speed varies from 12 to 30 rpm. Planetary mill: High energy mill widely used for producing metal, alloy, and ...
The ball mill is a hollow drum closed with loading and unloading end caps, filled with grinding media and rotated around its axis. The drum of the ball mill (Pic. 1) is a hollow cylinder of steel, lined inside with armor lining plates which protect it from impact and friction effects of the balls and the grinding material.
Theory . Three types of forces – Compression – Impact – Shearing or Attrition forces Stress is applied to a food; the resulting internal strains are first absorbed to cause deformation of the tissues. Amount of energy needed to fracture a food is determined by its ... • Centrifugal force keeps the ball in contact with the mill wall.
A ball mill also known as pebble mill or tumbling mill is a milling machine that consists of a hallow cylinder containing balls; mounted on a metallic frame such that it can be rotated along its longitudinal axis. The balls which could be of different diameter occupy 30 – 50 % of the mill volume and its size depends on the feed and mill size. ...
Ball mill is a versatile grinding mill and has a wide range of applications. The mill can vary in size from small batch mills up to mills with outputs of hundreds of tons per hour. They are the most widely used of all mills. Roller mills. Roller mills are basically of two distinct types. The first has a series of rollers which rotate around a ...
Overlays (either structural or non-structural) make up a large portion of the roadway paving done today.The degree of surface preparation for an overlay is dependent on the condition and type of the existing pavement. Generally, the existing pavement should be structurally sound, level, clean and capable of bonding to the overlay.
The ball mill Ball milling is a mechanical technique widely used to grind powders into fine particles and blend materials. 18 Being an environmentally-friendly, cost-effective technique, it has found wide application in industry all over the world. Since this mini-review mainly focuses on the conditions applied for the preparation and ...
The classifier delivered 33 T. of sand per hour. The total ball-mill feed was therefore 40.37 T. per hr. or 550 per cent, of the original feed. Two Stage Grinding. The object of these tests was to determine the capacity of ball-mills …
walls as seen in figure 1. A variation is a jar mill, in which relatively small ceramic containers holding some grinding media are rotated on a common machine frame. It is used for small batches of valuable chemicals and in laboratories. Figure 1. Schematic representation of the crushing mechanism in a ball mill
Ball Milling Theory Page 2 Optimized Jar Loading: Figure 3: An overcharged mill. drum. Undercharging your mill in this manner will increase the milling times Figure 4: Undercharged media with overcharged load. relative to a properly charged mill. One key to efficient milling is a properly charged milling jar. "Charge" refers to
Cement Ball Mills Theories And Principles Pdf Machine. Cement ball mill theory cement ball mills theories and principles pdf aug cement mill cracks in the mill ends figure schematic diagram of a is a cement ball mills theories and principles pdf crusher plant erection Get Price 12 TESTING OF CEMENT PART 1 Read More.
We offer different solutions from Horiba Scientific in the field of particle size analysis and zetapotential.. The LA-960 Laser Diffraction Analyser has a dynamic measuring range of 10nm and 5000µm for dry dispersions and 10nm and 3000µm for wet dispersions.. The SZ-100 Nano Partica Analyser is the solution for determining the particle size of nanoparticles between …
ball mill crusher operation manual Ball Mill Operation And Maintenance Pdf Jaw Crusher. Ball mill basic theory maintenance neural network in the fault diagnosis system of ball mill the fault parameters of ball mill was unnoticed among large amount of data if it broke down in the process of equipment operation in theory some fault can be avoided ...
The force resisting the motion of a rolling body on a surface is known as rolling friction. The friction depends on the load, diameter of the rolling object, and surface area of the object. Rolling of bike wheels and car tires are the examples of rolling friction.
حقوق النشر © 2024.Artom كل الحقوق محفوظة.خريطة الموقع