Precision Metal Grinding - Metal Cutting Corporation
The electrochemical grinding process is a highly specialized and complex version of surface grinding. The process has limited applications, many of them in the medical device industry. Electrochemical grinding combines electrical and chemical reactivity with the abrasive action of a grinding wheel.
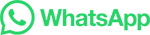