Grinding and Classifying Control & Automation - Sterling ...
Engineering and equipment are provided including electrical controls, classifying/grinding mill monitoring for safety and maintenance, sensors, and a PLC/PanelView-based automation system. These control and automation systems can also include formulation and setpoint data storage, live data trending, and historical data collection.
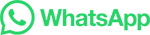