Make Black Powder Quick and Easy — Skylighter, Inc.
Removing Ball-Milled Black Powder "Mill Dust" from the Ball Mill Once the raw individual chemicals have been milled together and before further processing, the black powder is commonly referred to as "mill dust." Mill dust is an extremely flammable explosive. It is now time to separate the mill dust from the ball mill media.
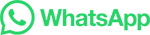