CEREC Primemill Tool Table
Wet Grinding Extra Fine: Glass, Hybrid, Feldspar Ceramics 67 14 062 Diamond 0,6 CS Wet Grinding Extra Fine: Glass, Hybrid, Feldspar Ceramics 67 14 054 Bur 2.5 ZrO2 CS Dry and Wet Milling: Zirconia 67 13 940 Bur 2.5 PMMA CS Wet Milling: PMMA, Composites, Plastics 67 37 469 Bur 1.0 CS
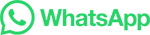