Air Pollution Control in the Cement Industry
From Control of Dust Emission in Cement Plants, R. J. PLASS, Mill Session Paper M-185 Portland Cement Association, Research and Development Division, 1966, 242 D. Technical and Legislative Control Difficulties 1) Technica1 - The problem of cement kiln exit gas dust:
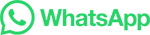