(PDF) SIZE REDUCTION BY CRUSHING METHODS
whereas grinding is generally performed wet and hence is more energy intensive. ... Quar tz, Diabase, Iron . Ore, Copper Ore, Zinc Ore and Manganese Ore. ...
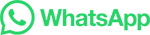
whereas grinding is generally performed wet and hence is more energy intensive. ... Quar tz, Diabase, Iron . Ore, Copper Ore, Zinc Ore and Manganese Ore. ...
Six steps to process iron ore 1. Screening We recommend that you begin by screening the iron ore to separate fine particles below the crusher's CSS before the crushing stage. A static screen is used to divert the fine particles for crushing. This step prevents overloading the crusher and increases its efficiency.
When processing natural fines from ores, the wet stage is started after crushing with the addition of large quantities of water. The wet stage begins at …
Raw material preparation varies depends on ore source, but typically involves crushing and grinding to reduce the size of the iron ore [19]. Moisture present in raw materials can create sticking ...
In the wet grinding process iron ore and water are mixed together and both are added to the mill in adjusted proportions performing a diluted grounded ore pulp. A large amount of water that is added to the grinding operation is removed by subsequent thickening, homogenizing and filtering stages.
Pyrometallurgical methods today employ high-temperature electric lab furnaces to process gold and silver ore samples, secondary scrap metals, and most platinum group metals. It uses 3 steps: Step 1: Preparation . The fire assay process begins by grinding samples into a fine powder to mix them with dry powder chemicals.
and the traditional dry grinding method was used as a reference. The effect of wet grinding on the activation of IOTs was evaluated through ion leaching from an alkaline solution and the reactivity index. Additionally, a detailed comparison between Dry-grinding Iron Ore Tail ings (DIOTs) and Wet-grinding Iron Ore Tailings (WIOTs) was made.
The ore will be crushed and processed at the site for the production of magnetite, dry process rejects, and wet tailings. The processing plant will use dry crushing and grinding circuit. The plant will employ the KB 63-130 type gyratory crushers, which will be the largest crushers in the country.
Download scientific diagram | Process flow sheet for Pelletization using wet grinding process from publication: Iron Ore Pelletization Technology …
12%Modern iron ore pelletizing process operations may be divided into two main process sections: feedstock preparation and agglomeration processes. In most plants, the required particle size distribution (PSD) is …
A process for upgrading low-grade magnetite-containing iron ore with minimum fine grinding. The dry ore is first comminuted to between about three-fourths inch and 10 mesh particle size and magnetically separated. The dry tailing is discarded and the concentrate is ground to between about 20 and 100 mesh and again subjected to dry magnetic separation.
Iron ore is the key raw material for steel production enterprises. Generally, iron ore with a grade of less than 50% needs to be processed before smelting and utilization. After crushing, grinding, magnetic separation, flotation, and gravity separation, etc., iron is gradually selected from the natural iron ore.
Dry processing normally goes from mining (extraction of the ore in the mine) up to sieving and crushing operations. When processing natural fines from ores, a …
The process uses coal gas for pre-heating & for partial reduction. Hematite / limonite / goethite ores get converted into magnetite ore in 1-10 minutes depending on the size of iron ore, at temperatures of 500-600 degree C. The left-over heat, after reduction, is utilized for 3 stage pre-heating of iron ore.
Iron ore minerals, particularly hematite and goethite, are beneficiated by a combination of size fraction, preconcentration, and flotation in stages (Fig. 13.45).Iron ore requires removal of silicate impurities of a finer size by flotation for higher-grade products of +60% Fe. ROM ore at 400–600 mm is fed to a primary crusher with product set at –40 mm.
The crushed ore is then transported to the mill site for crushing, grinding, classification and concentration. The second stage, grinding, is a wet operation which requires initial flotation and water to make a slurry. The hydrocyclone operates between each grinding operation to classify the type of particles: fine or coarse (Long et al., 1998).
Iron ore grinding process iron ore concentration process with grinding circuit dry the present invention discloses an advantageous and effective process for the concentration of iron ores which can be fully dry or mixed part of the process being dry part wet such enhancing the process efficiency as a whole by increasing recovery of.
Iron ore Benefication Process: 1.Large raw iron ore for primary crushing are fed into the jaw crusher by Plate feeder and are reduced to 8 inches or smaller. After first crushing, the material will transferred to cone crusher by belt conveyor for secondary crushing; the crushed iron ore stone will then transferred to vibrating screen for ...
Ball mills are used for wet grinding iron ore, g old/copper ore, nickel ore and other ores, as wel l as lime/limestone for flue gas desulphurisat ion systems, coal and other raw materials. Rod mill :
Fundamentals Of Iron Ore Wet Grinding - Oct 18 2012 More about Iron Ore Iron Ore Grinding. Iron Ore Grinding Process is an generated and discarded into the tailing pond disposal and use of iron ore tailings Coal processing system Dry magnetic separator for powder ore Wet magnetic more information about disposal and use of iron ore tailings ...
When the iron ore is extracted from the mine, it must undergo several processing stages. Six steps to process iron ore. 1. Screening. We recommend that you begin by screening the iron ore to separate fine particles below the crusher's CSS before the crushing stage. A static screen is used to divert the fine particles for crushing.
The Process would be generating any Hazardous Solid disposable waste which is also ideally suitable for brick making and would be delivered to local brick makers. 6.6. Noise level The Iron Ore Crusher & Ball Mil wet Grinding unit will be the major equipment where maximum noise generation will be taking place.
Those large mills operate either with water mixed in with the ore – called wet grinding – or without water - dry grinding. A fair amount of water is used in the wet grinding process. The material exiting the mills is in form of slurry with water content typically ranging from 30 to 50 %.
wet grinding process iron ore - Dripli. Iron Ore Processing Flowsheet Grinder Process. Iron ore processing depend mainly on the type of ROM ore feed and optimum product.Dry screening into lumps and fines is practised for high quality flaky ore and blue dust, because,if wet treatment is used, a substantial part of …
iron mining wet grinding process Iron ore processing depend mainly on the type of ROM ore feed and optimum product. Dry screening into lumps and fines is practised for high quality flaky ore and blue dust, because, if wet treatment is used, a substantial part of good quality material is rejected in the form of slimes
Beneficiation testwork by a relatively simple grinding and wet magnetic separation process yielded a grade suitable for use in the production of DRI (direct reduced iron) feedstock. Published resource is 3.69 billion tonne at 16%Fe making it one of the largest JORC-compliant iron resources in Australia.
wet vs dry iron ore mining – Grinding Mill Chinachinagrindingmill wet vs dry iron ore miningdry and wet process iron ore wet vs dry iron ore mining 171 views the is the professional mining e&cost of grinding by wet vs dry in iron ore
Iron Ore Processing Iron ore is the key raw material for steel production enterprises. Generally, iron ore with a grade of less than 50% needs to be processed before smelting and utilization. After crushing, grinding, magnetic separation, flotation, and gravity separation, etc., iron is gradually selected from the natural iron ore.
Grinding is a powdering or pulverizing process using the rock mechanical forces of impaction, compression, shearing and attrition. Main machines in ore grinding process are ore mill equipment. The most common iron ore grinding mills in mining are ball mill, Raymond mill and high pressure suspension mill.Jul 06, 2011 Iron ore grinding machine.
Some of the media falls and impacts the ore particles at the bottom of the mill. The rest of the media cascades and, in the process, creates particle breakage by attrition. The process is continuously repeated as the particles move by mass and volume action through the mill. Dry and wet grinding common.
حقوق النشر © 2024.Artom كل الحقوق محفوظة.خريطة الموقع