Manuals For Loesche Cement Vertical Mill
Loesche mill operation programdach-selbstreinigend . loesche vertical roller mills lm56 3 3 maintenance operation. loesche vertical roller mill operational manual Loesche Cement industry news from Global Cement The vertical roller mill uses a type LM 92 D mill it is designed for grinding are also in Loesche s scope of supply as well as a.
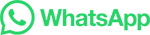