TPH =Tonnes per hour Normalized Thermal Energy …
32 THERMAL POWER PLANT - Under Perform, Achieve and Trade The formula for calculation of increase in energy consumption of Mills as a result of change in coal quality is mentioned below. Operating Hours (hrs) = Gross Generation (Million Units)X 1000/Operating load (MW)
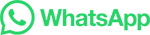