Mechanical properties of wood/plastic composites formed ...
The objective of this study was to investigate the mechanical properties of wood/plastic composites (WPCs) produced using wood flour (WF) prepared by wet ball-milling under various milling times (0–120 min) and drying methods (freeze- or heat drying). The drying method did not affect the particle size distribution, shape, or specific surface area of WF at …
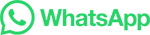