coal ball mill working principle used in pf boilers
Mathematic Modeling and Condition Monitoring of Power Station ... nonlinear Tube-Ball mill model for model based on-line condition ... the coal mill dynamics and can be used to predict the mill dynamic ... impact on power plant operation safety, which creates a potential fire ... components, e.g. mills, boilers and generators. ... mass flow rate of pulverized coal output …
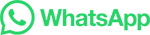