grinding abrasive process
GRINDING PROCESS. Grinding Process Grinding is a surface finishing operation where very thin layer of material is removed in the form of dust particles. Thickness of material removed is in range of 0.25 to 0.50 mm. Tool used is a abrasive wheel Grinding machine is a power operated machine tool where, the work piece is fed
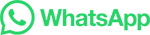