Installation, Inspection, Maintenance, and Repair …
ENVIRONMENT, SAFETY & HEALTH DIVISION . 26 October 2021 SLAC-I-730-0A21S-053-R005 1 of 8 . Chapter 14: Pressure Systems . Installation, …
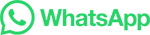
ENVIRONMENT, SAFETY & HEALTH DIVISION . 26 October 2021 SLAC-I-730-0A21S-053-R005 1 of 8 . Chapter 14: Pressure Systems . Installation, …
process and lab data available to production people, it also makes it available throughout the organization. By incorpo-rating process, business, maintenance and even planning data, KM is a critical component in total plant optimization and management. Functionally, what is also provided is …
Ball milling should be considered as a potentially attractive solution for solvent-free synthesis. 21 Solvent free One-pot process Tip of iceberg . Reference ... Andreas Theisen, "Green Chemistry"in the Laboratory, TECHNICAL REPORT,
Ball Milling - an overview ScienceDirect Topics. Ball milling, a shear-force dominant process where the particle size goes on reducing by impact and attrition mainly consists of metallic balls (generally Zirconia (ZrO 2) or steel balls), acting as grinding media and rotating shell to create centrifugal force.In this process, graphite (precursor) was breakdown by randomly striking …
3. Milling • Milling – A machine operation in which a work part is fed past a rotating cylindrical tool with multiple edges. (milling machine) • Types – Peripheral milling • Slab, slotting, side and straddle milling • Up Milling (Conventional) & down milling (Climb) – Facing milling • Conventional face, Partial face, End ...
The basic parameters used in ball mill design (power calculations), rod mill or any tumbling mill sizing are; material to be ground, characteristics, Bond Work Index, bulk density, specific density, desired mill tonnage capacity DTPH, operating % solids or pulp density, feed size as F80 and maximum 'chunk size', product size as P80 and maximum and finally the …
Ball Mill Working Principle. To be chosen according to the grinding material, material is composed of a ball mill feed end of the hollow shaft is arranged in the tube body, when the ball mill cylinder rotation time, grinding body due to inertia and centrifugal force, the effects of friction, making it attached to the cylinder liner on the cylinder body away, when taken to the height of a ...
CNC milling machine called CNC Baron Milling Machine (Figure 1.3) for 6,575USD. This machine claims to have 0.001'' (25.4μm) resolution and 0.00025'' (6.35μm) repeatability, which is significantly better than "Made-in-hina" machines. It also combines the
Milling machines may be manually operated, mechanically automated, or digitally automated via computer numerical control. Milling machines can perform a vast number of operations, from simple (e.g; slot and keyway cutting, planning, drilling) to complex (e.g; contouring,diesinking). Cutting fluid is often pumped to the cutting site to cool and ...
ball milling as a non-equilibrium processing method which can be analogous to rapid solidification. This review will first describe the equipment and some of the process va-riables used for high energy ball milling. Next, the physics of the milling processes has been described to the extent
Ball mill is a cylindrical device that used to grind and blend raw mate rials and it rotates around a horizontal axis, partially filled with the material to be ground plus the grinding medium. When...
charge motion. It is well known that ball milling efficiency varies during the lifetime of the shell liner. For instance, the mill performance could become worse or better by putting in a new shell liner. Data from pilot plant test work illustrates the influence of the shell lifting effect on the grind for a primary grinding duty.
The ball mill consists of a metal cylinder and a ball. The working principle is that when the cylinder is rotated, the grinding body (ball) and the object to be polished (material) installed in the cylinder are rotated by the cylinder under the action of friction and centrifugal force.
SHAPES ON BALL MILL PERFORMANCE Niyoshaka Nistlaba Stanley Lameck A dissertation submitted to the Faculty of Engineering and The Built Environment, ... Comminution is an important process in mineral processing, power plants, cement production and pharmaceutical industries. It is costly and an inefficient process in
The material in this manual was checked and deemed to be accurate. The entire risk as to its accuracy and quality is with the reader. In no event shall NexGen Manufacturing Systems, Inc. be liable for direct, indirect, or consequential damages resulting from any
Blasting is the process where small angular or spherical particles are propelled at a part by compressed air, or mechanical high speed rotating wheels or water pumps . The blast media type, shape, size, density, and hardness, along with media acceleration
The by-products in rice milling are rice hull, rice germ and bran layers, and fine brokens. V. MILLING SYSTEMS A rice milling system can be a simple one or two step process, or a multi stage process. In a one step milling process, husk and bran removal are done in one pass and milled or white rice is produced directly out of paddy.
In that work we employed a two-step process; 1) ball milling of silicon, and 2) spray pyrolysis of ball milled silicon in hexane at 1000± 1100℃ in an argon atmosphere. Silicon powder (99.99 %, particle size 0.05mm) was ball-milled in …
Unique conditions are milling using a planetary high-energy ball mill ("FRITSCH" the great attractive interest for researchers due to the model Pulverisette 6) at 200 rpm rotating speed for 4 hours. control of the microstructure during the synthesis of ma- After milling, a total of 9.2 g of sample was recovered, and terials by mechanical ...
The mill consists of a rotating shaft with four attached parallel knives and a screen occupying one fourth of the 360 degree rotation. The mill is best used to crack whole grains with a minimum of "fines". It is not used as a final process for reducing the …
A material removal process in which a sharp cutting tool ... Machine tool called a milling machine ... Ball-nose cutter is fed back and forth across the work along a curvilinear path at close intervals to create a three dimensional surface form Figure 22.20 (f) surface contouring
The ball mill Ball milling is a mechanical technique widely used to grind powders into ne particles and blend materials.18 Being an environmentally-friendly, cost-effective technique, it has found wide application in industry all over the world. Since this mini-review mainly focuses on the conditions applied for the prep-
For any process, including ball mill circuits, we can say that output equals input multiplied by efficiency*. Output = Input x Efficiency In a ball mill circuit, the "output" can be defined as the production rate of fines of the circuit. As for any output, ball mill circuit output is a function of both its inputs and efficiencies.
A machining process defines a process in which a piece of raw material is cut into a desired final shape and size by a series of machining operations. Common types of milling operations include the following: Side Milling Facing Slotting Plunging & Pocketing Ramping Machining of an edge surface on the part. Machining of a top face on the part.
Figure 8.5 Effect of mill filling on power draft for ball mills. The data is taken from Rexnord Process Machinery Reference Manual, Rexnord Process Machinery Division, Milwaukee, 1976 The effect of varying mill speed on the power drawn by the mill is shown graphically in Figure 8.4
- Technical books of electric machines - Freely accessible internet resources For quick orientation Table 1 gives a brief comparison between the different machine types. The statements refer to a typical design from each type. The
Version 1.0, November 2019 . Standard Operating Procedure . FRITSCH. Pulverisette 7 Ball Mill . Yale West Campus Materials Characterization Core
Scientific, technical publications in the nuclear field | IAEA
Burrs generated along the finished edges and surfaces in micro-milling operation have significant impact on the surface quality and operational performance of the finished parts and microstructures. In order to obtain a better recognition of burr generation process, 3-dimensional micro-ball end milling operation FEM models on Ti–6Al–4V have been …
Contact Thrust Ball Bearings 2344, 2347 Angular Contact Thrust Ball Bearings for Ball Screws 7602, 7603, BSB DBSB DBSBS Axial-Radial Cylindrical Roller Bearings RTC Engineering Appendix P. 12 P. 78 P. 80 P. 84 P. 86 P. 94 P. 102 P. 104 P. 112 P. 114 P. 120 P. 124 P. 128 P. 130 P. 4 P. 8 P. 134 P. 182 FAG-Hong Kong Eric Bearing Co.,Ltd, Web Site ...
حقوق النشر © 2024.Artom كل الحقوق محفوظة.خريطة الموقع