Cement Manufacturing Process | Phases | Flow Chart ...
This saves the extra fuel cost and makes cement somehow economical. Raw materials are extracted from the quarry and by means of conveyor belt material is transported to the cement plant. There are also various other raw materials used for cement manufacturing. For example shale, fly ash, mill scale and bauxite.
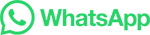