Mineral Processing - SlideShare
Attrition between grinding balls and ore particles causes grinding of finer particles. SAG mills are characterized by their large diameter and short length as compared to ball mills. The inside of the mill is lined with lifting plates to lift the material inside the mill, where it then falls off the plates onto the rest of the ore charge.
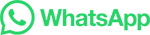