Ball Mill,Ball Press Machine,Dryer Machine,Ring Die Pellet ...
Ball Mill Accessories. Generally, ball mill accessories include durable steel ball, steel forging, high alumina ball, ceramic ball, ball mill plate and so on. Learn More; Flotation machine. Flotation machine or flotation separator is used to separate non-ferrous black metal (like copper, zinc, lead and gold) and nonmetal like fluorite and talc.
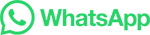