Grinding Machines – ORSKOREA
Grinding Spindle: Hydro-Static or Roling Bearing Type: Spindle Height: About FL 1150: Work Spindle RPM: 150 to 1800 rpm: Grinding Wheel Spindle RPM: MAX. 2,200 rpm (3,000 m/min) Outer Dimension: 2100 * 1900 * 1950H: Weight: 5.5 Ton: Hydraulic Tank Capacity: 40 Liter
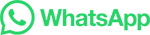