Material Balance On Cement Mill - theroadtrippers.in
Material Balance Around Raw Mill In Cement. The balance of the ball mill cement. the balance of the ball mill cement the balance of the ball mill cement stone crusher machine A cement mill is the equipment used to grind the hard nodular clinker from the cement is currently ground in ball mills and also vertical roller mills Cement mill From ...
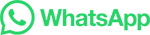