cement summary | Britannica
By The Editors of Encyclopaedia Britannica. Below is the article summary. For the full article, see cement . cement, Agent that binds concrete and mortar. Cements are finely ground powders that, when mixed with water, set to a hard mass. The cement of 2,000 years ago was a mixture of ash and lime. Volcanic ash mined near the city of Puteoli ...
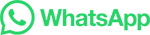