Classification of Grinding Machine - YouTube
In this video, I explained Classification of Grinding Machine.= = = = = = = = = = = = = = = = = = = = = = Video link:Grinding Machine: Classification of Gr...
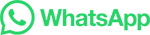
In this video, I explained Classification of Grinding Machine.= = = = = = = = = = = = = = = = = = = = = = Video link:Grinding Machine: Classification of Gr...
tapered grinding rollers, arranged at an angle of 15° to the grinding table. • Hydraulic grinding roller swinging-out device for easier and quicker changing of grinding components. • Constant product quality in compliance with specification achieved through static or dynamic classification. • Product rate control from 40 to .
It is a very thin cup-style grinding wheel which permits grinding in crevices and slot. Saucer Grinding wheels: Saucer Grinding Wheel is an exceptional grinding profile used for grinding twist drills and milling cutters. This finds wide usage in non-machining areas, as these saw filers are used by saucer wheels to maintain saw blades.
These grinders are used for grinding round and hollow jobs whether the internal surface of this job is completely round, ditched round, or is in taper. Small grinding wheels of 3 cm to 5 cm, are used in such grinders. Sometimes grinding wheels of special shape 0.2 cm to 0.3 cm. These grinders can be divided into two parts. a. Chucking Grinder
13) Welding, Gas Cutting & Grinding 14) Sand Blasting / Abrasive Blasting 15) Road Work-Widening Project (Flexible Pavement / BC Pavement) 16) Roof Works 17) Confined Space 18) Radiography 19) Tower Erection and Stringing 20) Working Near IR Track 21) Under Ground Tunnel Work 22) Working Over or Adjacent to Water
Grinding Grinding is the most common form of abrasive machining. It is a material cutting process that engages an abrasive tool whose cutting elements are grains of abrasive material known as grit. These grits are characterized by sharp cutting points, high hot hardness, chemical stability and wear resistance.
©2002 John Wiley & Sons, Inc. M. P. Groover, "Fundamentals of Modern Manufacturing 2/e" Classification of Machined Parts 1. Rotational - cylindrical or disk-like shape 2. Nonrotational (also called prismatic) - block-like or plate-like
• Grinding ±0.008mm • Lapping ±0.005mm Surface finish, roughness Casting • Die Casting Good 1-2µm • Investment Good 1.5-3 • Sand Casting Poor 12-25 Metal forming • Cold rolling Good 1-3 • Hot rolling Poor 12-25 Machining • Boring Good 0.5-6 • Drilling Medium 1.5-6 • Milling Good 1-6 • Turning Good 0.5-6
to diameter. The vessel is charged with the grinding media. The grinding media may be made of hardened steel, or tungsten carbide, ceramics like agate, porcelain, alumina, zirconia. During rolling of vessel, the grinding media & powder particles roll from some height. This process grinds the powder materials by impact/collision & attrition.
Application examples, specific energy for grinding (related to complete system) 1200 AWM with Natural Fineness 99 % < 100 µm integrated gypsum Throughput 16 t/h Micron Classifier MS 4 Espec. < 12 kWh/t 960 AWM with Dolomite Fineness 97 % < 63 µm integrated Throughput 2,7 t/h
Grinding machine is a type of machine tool and it is similar to other machine tools such as milling machine, turning machine, Lathe Machine and many more. The major difference between Grinding machine and other conventional machine tools is the type of operation and method of machining. Generally, all the machining process removes material from ...
In centerless through feed grinding, which is a typical serial grinding process, pistons for the automotive industry, shafts, rods and also elements for the rolling bearing industry are produced. Internal cylindrical grinding: Internal cylindrical grinding is one of the most common and also most difficult grinding operations.
use classification with spiral classifiers. 5.0 Types of Crushers: A crusher is a machine designed to reduce larg e rocks into smaller rocks, gravel, or rock dust.
• Grinding stock feed • Classifier speed • Mill fan speed • Water spraying • Hot gas • Fresh air Manipu-lated variables Disturbance variable Process measured value 1402782_Relauch_LMmaster 6 25.08.14 11:47. 7 Optimisation limit Limit with conventional control Optimisation potential
On grinding machines, these operations are best done with a diamond dressing tool rigidly supported in a fixed tool post. Abra-sive wheel dressers and abrasive type dressers are used on bench or pedestal grinders. 4-CUTTER TYPE DRE TUBE TYPE DRESSER RA PD 87178 6. TM 9-867 1. Set tool as shown, almost ...
Grinding Wheel in Industry. A vitrico grinding wheels is the most common equipment in the metallurgy industry. Grinding Wheel cuts metals with different sizes, shapes, and efficiency. Grinding Wheel is generally composed of two types of materials
9.10.1.1-2 EMISSION FACTORS 6/97 Figure 9.10.1.1-1. Simplified process flow diagram for cane sugar production. (Source Classification Codes in parentheses.)
Grinding is the process of removing material by the cutting action of the countless hard and sharp abrasive particles of a revolving grinding wheel as they come in contact with the surface to be ground. Grinding machines are made in a variety of types and sizes, depending upon the class of work for which they are to be used.
grinding chamber wall, classifier wheel, and conveying line. This can reduce mill capacity and air classifier performance. Particle surface chemistry can affect many material proper-ties that affect flow, including stickiness, affinity for water, and tendency to accumulate electrostatic charge. The flowability of the feed material dictates ...
WHITEPAPER 3 A basic guide to particle characterization Particles are 3-dimensional objects, and unless they are perfect spheres (e.g. emulsions or bubbles), they cannot be fully described by a single dimension such
Grinding flat or plane surfaces is known as surfaces grinding. Two general types of machines have been developed for this purpose; those of the planer type with a reciprocating table and those having a rotating worktable. Each machine has the possible variation of a horizontal or vertical positioned grinding wheel spindle. The
Grinding 1. Grinding and Grinding Machine 2. Grinding: Grinding is a process of removing material by abrasive action of a revolving wheel on the surface of a work-piece in order to bring it to required shape and size The wheel used for performing the grinding operation is known as grinding wheel It consists of sharp crystal called abrasive held together by a …
5. Other Machining Operations • Shaping and planing – A single-point tool moves linearly relative to the work part – Shaping - A tool moves
C. Hydrometer Testing (for fine−grained soils: 0.5µm < D < 75 µm) It is assumed, as a first approximation, that fine−grained soil particles can be idealized as small spheres.
Tool and cutter grinding machine: These are the special types of grinding machines which are used for the machining of cutting tools which are used for milling, turning and drilling operations. The grinding of a tool has two parts i.e. manufacturing of new tool and re-sharpening of an old tool. The simple single point cutting tool which is used in turning is …
CENTERLESS GRINDING • Centerless grinding is a machining process that uses abrasive cutting to remove material from a workpiece. centerless grinding differs from centered grinding operations in that no spindle or fixture is used to locate and secure the workpiece; the workpiece is secured between two rotary grinding wheels, and the speed of ...
Fine grinding or milling reduces the particle size down to as low as 1.0 micrometer (µm) (4 x 10-5in.) in diameter. Ball mills are the most commonly used piece of equipment for milling. However, vibratory mills, attrition mills, and fluid energy mills also are used. Crushing and grinding typically are dry processes; milling may be a wet or dry ...
GRINDING (Abrasive machining) Grinding is a surface finishing operation where very thin layer of material is removed in the form of fine dust particles. (thickness 0.25-0.5mm) Grinding can be defined as a material removal process by the abrasive action between rotating abrasive wheel & the work piece.
3 OVERVIEW • Role of resins in FRP composites • Thermosets vs. thermoplastics – Advantage & limitations • Polymer chemistry – Chain & step polymerization • Catalysts, inhibitors, accelerators – Chain crosslinking/ curing – Typical thermoset resin systems • Polymer processing • Polymer physics – Glass transition – Stress-strain curve • Summary
Cutting Tool Applications, Chapter 17: Grinding Methods and Machines. June 29, 2020. Grinding, or abrasive machining, once performed on conventional milling machines, lathes and shapers, is now performed on various types of grinding machines. George Schneider. Start Slideshow.
حقوق النشر © 2024.Artom كل الحقوق محفوظة.خريطة الموقع