1-Improving Grinding Efficiency | PDF | Performance ...
1-Improving Grinding Efficiency - Free download as Powerpoint Presentation (.ppt / .pptx), PDF File (.pdf), Text File (.txt) or view presentation slides online. Scribd is the world's largest social reading and publishing site.
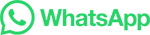