Industrial Solutions polysius ball mills
• Mill inspection via the inlet is possible, thus increasing personnel safety • Less wear and simpler form of wear lining on straight end walls • Short inlet cone • Less bearing clearance and thus less mill shell deflection polysius ® ball mill with direct drive There are two types of gear unit available for the mill drive unit.
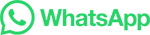