OSTI.GOV Technical Report: IMPROVING ENERGY EFFICIENCY VIA ...
The actual SAG mill power draw is 230-370 kW lower. Mill runs 1 rpm lesser in speed on the average. The re-circulation to the cone crusher is reduced by 1-10%, which means more efficient grinding of critical size material is taking place in the mill.
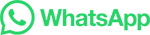