Advanced Controller for Grinding Mills: Results from a ...
The ore from the bins is fed into the ball mill using a conveyor belt. The ball mill grinding circuit is illustrated in Figure 2. % Solids 78.9 Circulating Load 474% Advance Control Optimizer Manual Mode Preset Output Alarm Summary 6 Mills Display Group Display sump level: 86.4% 13.1 AMPS Primary Ball Mill No. 5 Solids, Flow GPM 66.7 % 1.72 9.1 ...
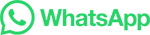