Ball Mill Used in Minerals Processing Plant | Prominer ...
This ball mill is typically designed to grind mineral ores and other materials with different hardness, and it is widely used in different fields, such as ore dressing, building material field, chemical industry, etc. Due to the difference of its slurry discharging method, it is divided to two types: grid type ball mill and overflow type ball mill.
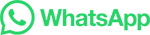