Dry Granulation: The Definitive Guide - SaintyTec
As the milling equipment rotates breaking ribbon or flakes into smaller particles, there are three possibilities: Size of particles that are bigger than what you need; Average size of granules you need; Very fine particles, that are of equal size of the powder; This is how the roller compactor machine manufacturers ensure there is a high ...
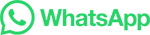