Role of Chemical Additives in Stirred Media Mill Grinding
(media and,particles) concentration was fixed at 75%, corresponding to a particle solid concentration of 44% by volume. The results obtained for average energy efficiency vs. additive concentration are shown in Figure 1, These results for stirred media mill operation correspond to conclusions drawn in earlier
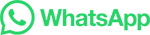