Introduction to Mineral Processing
composition and treatment of metals are varied to provide desired physical and mechanical properties. In mineral processing, a number of unit operations are required to prepare and classify ores before ... crushing or the grinding circuit.
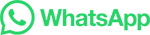